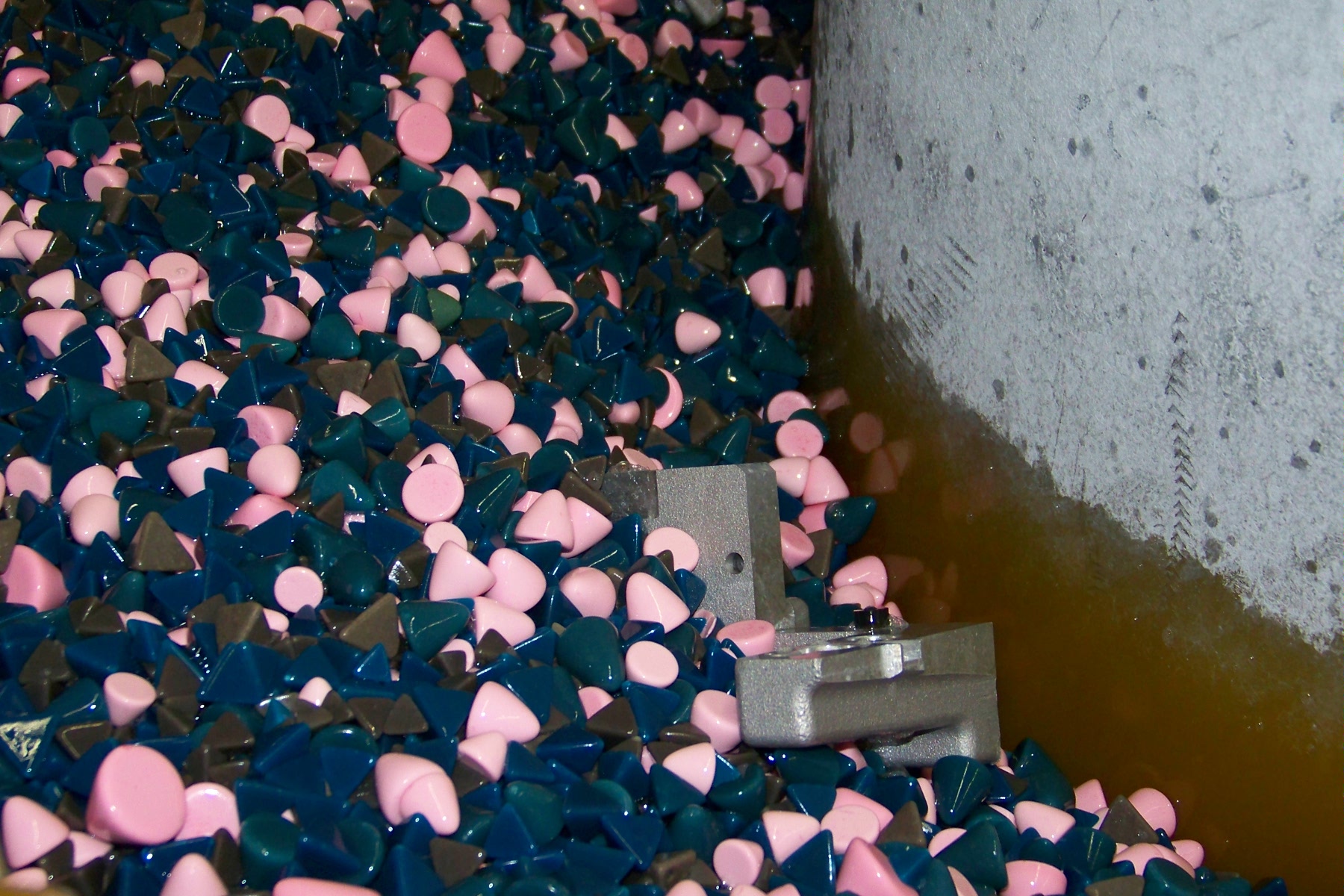
14 Sep Tumble vs. Vibratory Finishing
Tumble vs. Vibratory Finishing: A Comprehensive Guide
Mass finishing is the go-to solution for large batches of parts and components that need deburring, polishing or similar uniform surface finishing. In addition to a standardized finish for each individual part, utilizing the finishing process also strengthens them against wear and corrosion. In general, the most popular methods of mass finishing are tumble finishing — also known as barrel tumbling or barrel finishing — and vibratory finishing.
What Is the Tumble Finishing Process?
The tumble finishing process uses a rotating horizontal barrel, water or another lubricating agent and various types of abrasive media to deburr, remove rust or polish parts. This method results in a smooth, polished finish and is used for many metal and plastic components that can hold up to the abrasion process. Many industries make use of the tumble finishing process, including the automotive and construction industries.
Benefits of Tumble Finishing
There are a number of benefits to the tumbling finishing process, including:
- Lower cost
- More consistent than hand finishes
- Increased part strength and durability
- High efficiency
- A full cycle only takes between 6 and 26 hours to complete
- Large volume capability
- Versatility of process
- Different media, additives and compositions can be used to create many different finishes
While not ideal for all applications, tumble finishing offers a robust, easily repeated outcome that is perfect for many heavy-duty projects.
What is Vibratory Finishing?
The vibratory finishing process uses a vibrating bowl or tub along with various media and compounds to abrade parts. Similar to tumble finishing, this process removes edges and burrs and can achieve a number of different finishes. Vibratory finishing can also be used as a preparatory step for parts that will eventually be plated or used for adhesion. In addition to the various industries that use tumble finishing, vibratory finishing can be used in the medical industry, where a more delicate process is required to maintain the viability of the parts.
Vibratory finishing can be done either wet or dry, although many people prefer the wet method because it produces a smoother, more polished finish.
Benefits of Vibratory Finishing
Vibratory finishing offers a number of benefits for your parts, such as:
- Increased part lifespan and durability
- Process can be automated for greater efficiency and consistency
- Large volume capacity
- Compatible with a wide variety of part materials
- Sensitive design maintains part integrity
- Designed to handle large or delicate parts
- Water from the wet process can be recycled
Making the Right Choice for Your Metal Finishing Needs
When deciding between tumble and vibratory finishing, it’s important to consider a number of factors. Cost is an obvious thing to take into account, but just as important are the material characteristics of your components, the desired finish and the eventual use of the parts.
Evaluating Material and Component Characteristics
Knowing your materials is key in choosing the best finishing method for your parts. On the whole, parts made of tougher, heavier metals that won’t be used in tight-tolerance situations stand up better to tumble finishing, while parts that require more precision or are susceptible to surface damage are better suited to vibratory finishing.
Desired Finish Quality and Consistency
Take the time to consider the end finish of your parts, as well as how achieving that finish will affect their makeup. A very smooth finish can be achieved with tumble finishing, but the amount of wear will be much higher than if you use a vibratory finishing process, leading to shorter lifespan and less durability. Additionally, take into account the aesthetic needs of your parts. The more polished and pristine you need the finish to be, the more likely it is that vibratory finishing is the most suitable choice.
How Do I Choose Between Tumble and Vibratory Finishing?
When making the final decision on the best finishing process for your parts, it is vital you consider their end function and composition alongside your desired finish and budget. Vibratory finishing is the most popular process used today, but that doesn’t mean it is right for every project. Take the time needed to account for all the variables that could affect your parts and if you need guidance, don’t hesitate to reach out to our expert team.
Want more information? Learn more about our approach to mass finishing.