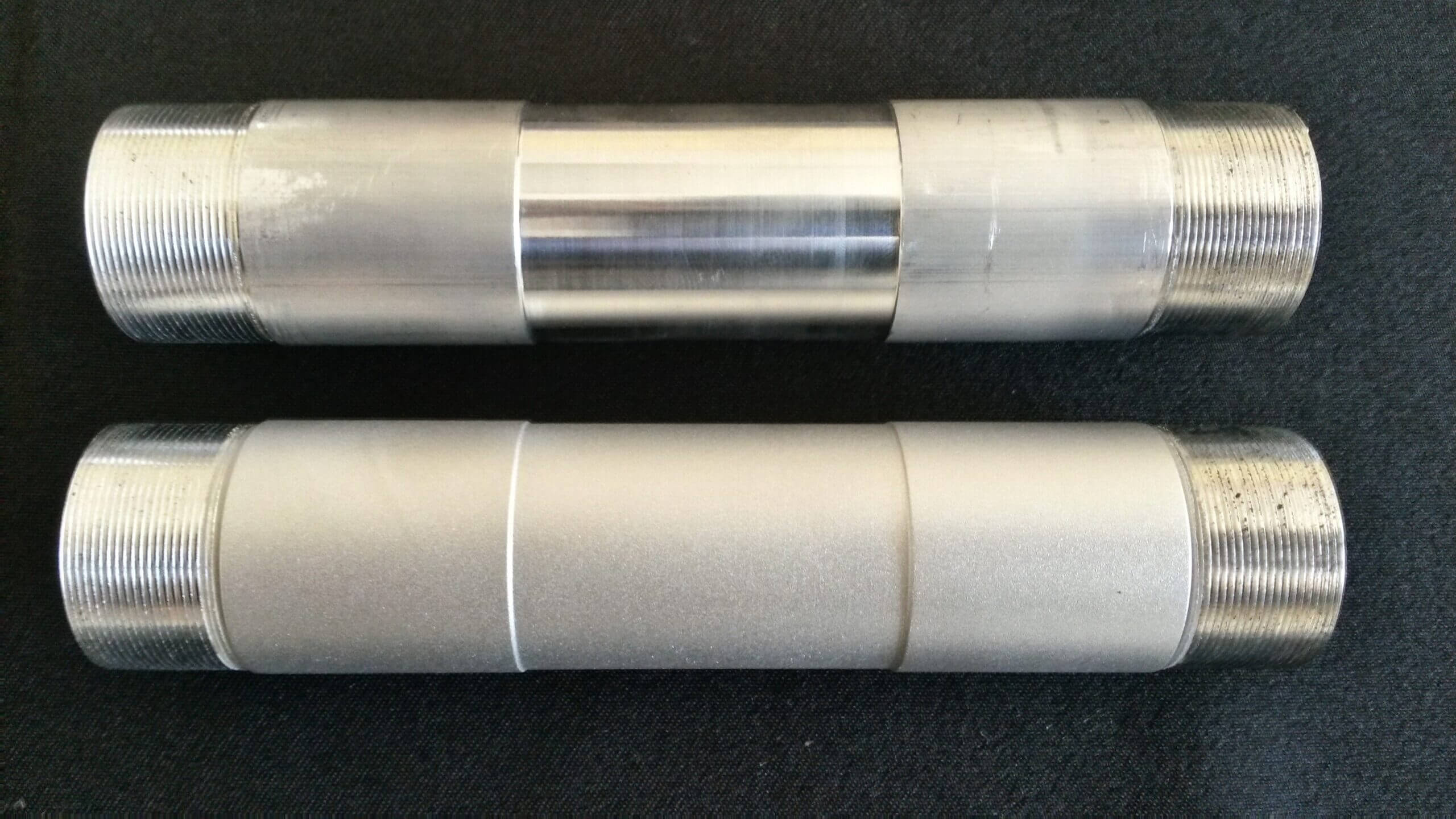
06 Dec Transforming Aluminum Surfaces
A Guide to the Process of Bead Blasting Aluminum Surfaces
Finishing aluminum parts with bead blasting is a convenient, effective way of ensuring your components get your desired finish, are more protected against fatigue damage like cracking, and are prepared for any secondary finishes that may be required.
How Does Bead Blasting Aluminum Work?
To put it simply, bead blasting works by firing small beads of media, made of materials like glass or steel, against the surface of parts at high pressure, resulting in a uniform finish. The bead blasting process strengthens aluminum components and improves their overall longevity.
Choosing the correct media
The size and material of the media used to bead blast aluminum will affect the components differently, so the all-important first step is to determine what the required end result will be.
For example, smaller media can produce brighter finishes with satin textures, while using larger media will result in rougher, if still uniform, finishes. Glass media will not affect the color of the substrate, which can help retain a higher polish, while steel and other materials may darken the color slightly, especially when using larger sized media.
Blasting the aluminum parts
After the size and type of media are selected, the components are put into a durable blast cabinet and the operator uses a blaster gun that propels the media at high pressure against the surface of the components. This process can take time on larger surface areas or for rust removal, but the precision provided by bead blasting is excellent for consistent, reliable results.
What Is Aluminum Bead Blasting Used for?
A wide range of aluminum components can benefit from bead blasting, and the process is used in various industries. It’s particularly useful for aluminum due to its ability to clean or create a surface finish without removing significant material or altering the dimensions of the part.
- Aerospace: The aerospace industry frequently uses bead blasting for finishing aircraft components. It’s essential for ensuring a smooth, clean surface which can be critical for both aerodynamics and the integrity of the parts.
- Manufacturing and Machinery: Various machinery parts made of aluminum require bead blasting to ensure a clean, finished surface. This is important for both the performance and longevity of the machinery.
- Defense and Military: The military sector uses bead blasting for finishing various aluminum components in vehicles, weapons, and other equipment. This process is crucial for ensuring that parts meet the strict standards required for military use.
- Automotive: In the automotive sector, bead blasting is used for finishing aluminum parts such as engine components, wheels, and decorative trim. It helps in removing surface contaminants and preparing parts for further processes like painting or anodizing.
- Electronics: For electronic components, particularly those made of aluminum, bead blasting is used to ensure a clean, conductive surface. It’s also used in the manufacturing of enclosures and heat sinks.
- Medical Devices: The medical industry uses bead blasting for finishing surgical instruments, implants, and other devices made from aluminum. This process ensures that the surfaces are free from contaminants and have the necessary texture for their intended use.
- Marine: In the marine industry, bead blasting is used to clean and prepare aluminum parts for boats and ships. This includes components like hulls, masts, and deck fittings, where a clean, corrosion-resistant surface is essential.
- Construction and Architecture: Bead blasting is used in the construction industry for finishing aluminum components used in buildings, such as frames, panels, and decorative elements. It provides a uniform, aesthetically pleasing finish.
Any aluminum parts that require cleaning, deburring, peening or a uniform, professional-looking finish are great candidates for Eaglemaster’s bead blasting service.
Bead blasting can also be used for preparing aluminum components for various post-finishes, including powder-coating and painting, allowing for an even wider range of applications.
The Importance of Bead Blasting in Aluminum Finishing
When deciding whether bead blasting is the ideal finishing process for your aluminum components, it’s worth taking the time to understand the broad benefits and potential downsides.
Benefits of bead blasting aluminum include:
- Cost-effective
- Ecologically friendly — media can be reused multiple times before needing to be replaced, especially glass media
- Surface cleaning and preparation
- Uniform finish
- Enhanced adhesion
- Removing burrs and sharp edges
- Corrosion resistance
- Precise
- Safe for operators
- Suitable for more delicate components without harming the aluminum
Considerations to keep in mind:
- Bead blasting can be time-consuming for larger parts
- Line of sight is required, so parts with intricate details or interior finishing requirements can be difficult to work with
- Not ideal for applications requiring tight tolerances
- Not an automated process
If you are unsure whether bead blasting is the right choice for your aluminum components, our team of experts is here to help and answer any questions you have.